|
Post by mlehman on May 24, 2015 21:10:24 GMT -8
Not much is really new here if you've been around the hobby for awhile. How do you get a cheap and easy turntable if you don't want another Atlas coffeegrinder? You make one from a 1/4" phone plug and mating jack. It may have sounded intimidating, but it's really not. It's so cheap to do one, consider taking a stab at it. I estimate $20, because you'll spend about $10 on the plug and jack (you actually get 2 in each package from Radio Shack, so you will have parts to build 2) and the other $10 is my rough estimate of a piece of track, various bits of wood, wire, some plastic girders, etc, but depends on what you find in the scrapbox, too. Here's some pics and advice from the two I've built. First of all, you need a level spot for not just the turntable but the finger tracks, too. Otherwise, it's too easy for stuff to end up in the pit. An alternative to a level spot is to build everything up so it's level. My first TT site wasn't very level but I used wood and cork to build it up  You also need a piece of thin material to form the bottom of the TT pit. It must be thin because you need to be able to mount the jack in the middle of it. Most jack's I've seen have about a max of 1/4" range for what they're mounted in, because most of the time they're in a thin metal case. I used 1/8" Masonite for the first pit and 3 pieces thick of aluminum flashing for the second, each maybe .010" thick. This pit material can be screwed or glued to the underlying framework, in both case wood for me. It's should be possible to mount one of these turntables in foam, but you'll need to let the glue set-up before proceeding at each stage. My second TT site was underlaid with a mix of wood and foam, overlaid with Sculptamold. I drilled a strategically placed hole in a piece of wood to clear the plug underneath the TT pivot and electrical contact. 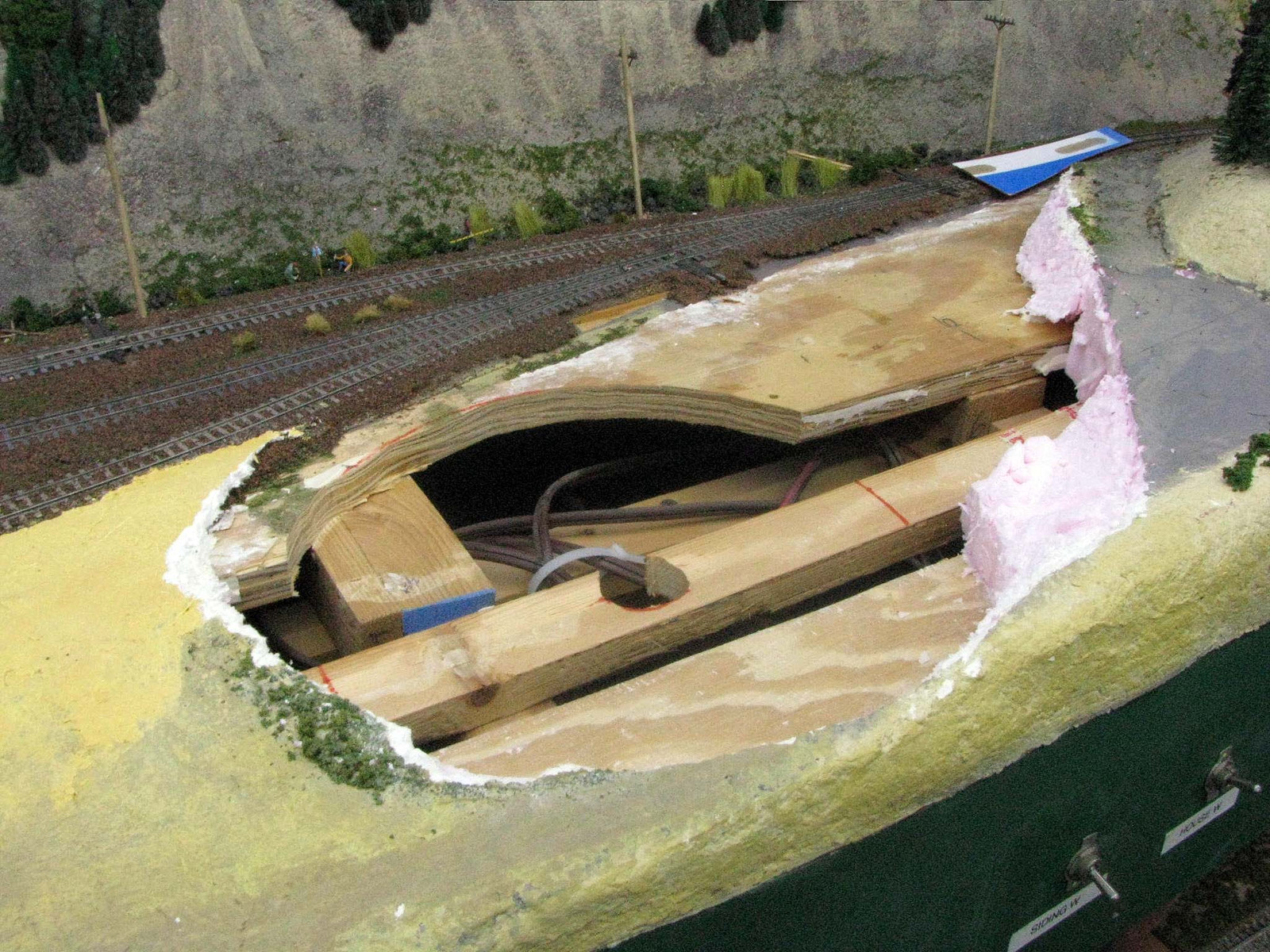 The depth here was around 3/4" to the wood support underneath, basically level with my 3/4" ply subroadbed. This measurement is critical, because it, plus the height of your roadbed and track determines the height of your TT bridge. I use basswood or balsa for both my bridges. The upper piece is as long and wide as your TT needs to be. The lower piece is shorter and acts to provide a mount for the 1/4" phono plug. Here's look at it in raw form.  And from the side. Note the two blocks that act as sliders to support the ends. In this design, the wheels that are added later are strictly ornamental, it's actually these blocks that do the work , so it's best they are hardwood, not balsa or even pine, which would wear away. I epoxy on two small washers to take most of the wear. 
|
|
|
Post by bnsf971 on May 25, 2015 3:12:44 GMT -8
It looks good. Just don't use a blender motor to power it...
|
|
|
Post by mrsocal on May 25, 2015 5:34:49 GMT -8
Smart use of the ol headphone jack. I like it.
|
|
|
Post by nebrzephyr on May 25, 2015 5:45:08 GMT -8
Mike....I see only one problem....finding a Radio Shack store anymore.  Bob
|
|
|
Post by mlehman on May 25, 2015 6:55:56 GMT -8
Terry, This is an eco-friendly, 100% zero emissions, and sustainable turntable. No blenders, etc, just your finger powers it. For the perpetually dissatisfied and grouchy among us, use of the middle finger is allowed (although only off-camera, please!).
Scotty, Yes, and if you do recycle an old jack and plug, it's even cheaper. I'm sure someone will chime in to say I paid too much and the phono plug industry is just ripping us off, so that's a way to get it cheaper.
Bob, That could be a problem; there are other sources for the parts, although the Shack was always in the 'hood. Ours is still open and I think they've closed a deal for the tired old bones of RS, so maybe things will stabilize. The plug I used is a sorta new item from RS, a plug with a very fat, heavy duty body that makes it much easier to have a strong and level bridge. I'll dig the part number of it specifically out eventually here. I know I bought the last pair in town here, so hope they do restock when the dust clears.
|
|
|
Post by mlehman on May 25, 2015 7:05:33 GMT -8
Just to further consternate Scotty, I whipped this together after my SPF posts yesterday...  Well, not really, it was more of a fixer upper from my youth, circa 1972. Here's the condition it was in after 40 years of traveling back from Germany and hanging out in a box. The warppage is not so apparently in the pic, but there was hardly a truly straight board on it. 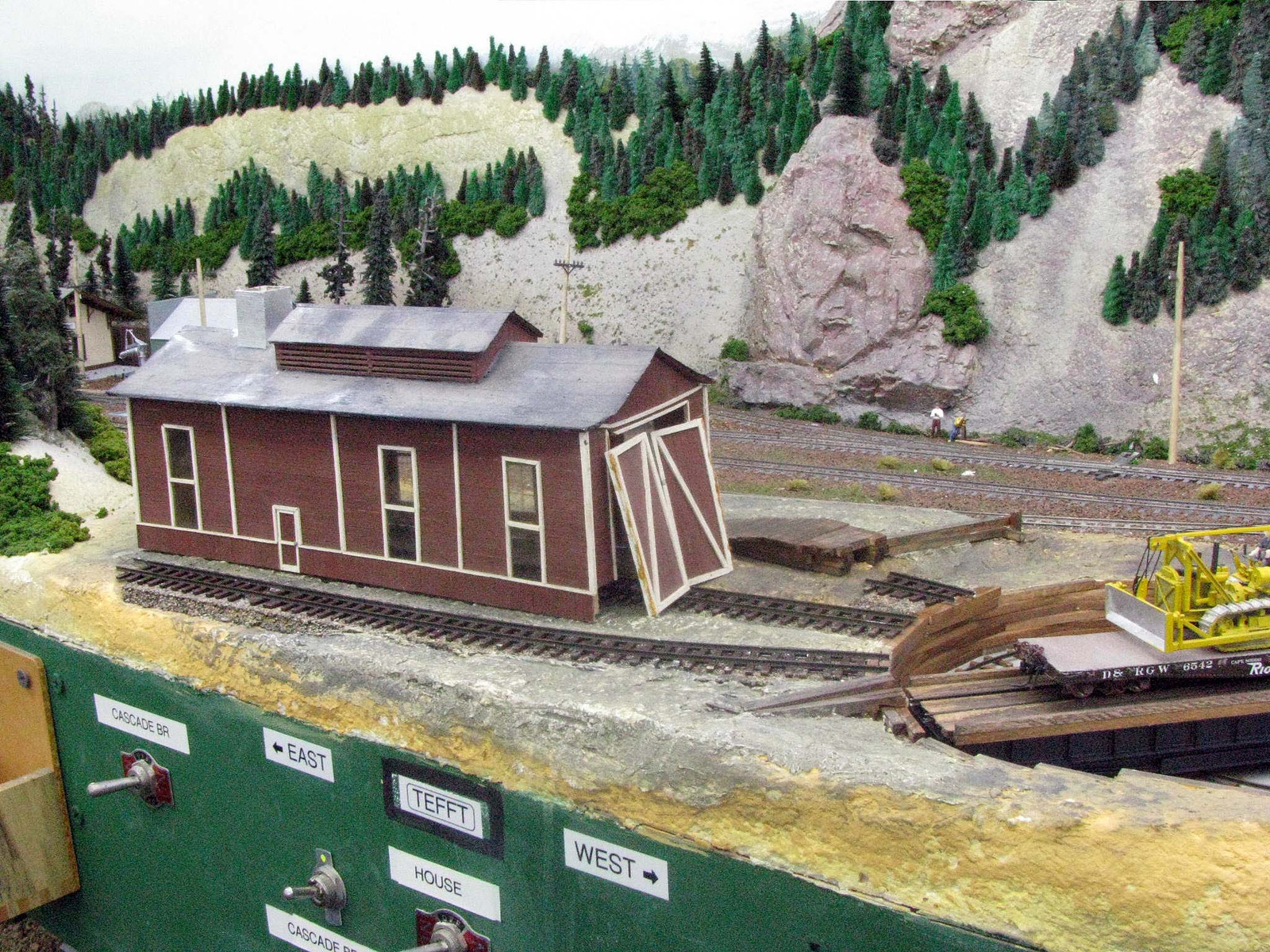 There was a lot of work in that. It's mostly balsa, which I cut most of the stock myself, with a little clear plastic and some paper roofing. I managed to save all the bigger vital pieces, but lost a bit of wainscoting. No problem, it should have a stone foundation anyway. A new set of hinges for the doors, fix the smokejack cover and we're in business. It needs a couple of new windows and they all need new mullions. I think these were inked or scribed and ink and that has faded badly. Not sure about the roof, starting to liek the old tapaper, but may apply tin roofing paper (which I have) or laser shingles (which will have to wait because I'd have to buy). Also needs a floor, but is otherwise pretty shipshape for what it's been through.  So most of the work was done and about 3 hours of bracing and fixing up yielded a pretty darn nice enginehouse. I think I built it from a plan, but can't recall which one. Thought it was in Willard Anderson's Kalmbach structure plans book, but it wasn't.
|
|
|
Post by mrsocal on May 25, 2015 8:06:19 GMT -8
It all looks really nice together, but... that pit looks like a band new concrete slab. Need some stains and drippings down in there my friend. Just a thought. :-)>
|
|
|
Post by mlehman on May 25, 2015 8:09:19 GMT -8
Lost this last night, so will hurry through before the computer pukes out again. Please feel free to ask questions about anything, as I may gloss over something important you find you need to know. The first bridge was layers of masonite and basswood luaun. The second was soft pine. Balsa could be used, but may be more fragile depending on your skills. The top block needs to be roughly the length and width to suit, while the smaller needs to have a hole drilled to accommodate the phono plug, which is installed through it. It is then attached to the upper block, with the wires to the plug leads passing through it (you did remember to solder leads to the plug, didn't you?) It's a standard 1/4" mono plug. No need for stereo here.  And upright and plugged in  You'll notice the blocks that project down on each end with the tiny washers attached. These are what holds the ends level, so cut the accurately once you've laid the outer ring rail. Nickel-silver rail is very flexible with a little care, so form and solder a rail joiner to hold them together. I could've used more ties under the rings rails on my first TT. Also, the inner ring rail is strictly cosmetic, nothing rides on it.  Here's what things look like with the cosmetic wheels in place on the end blocks. It should be noted that the outer ring rail needs to be roughly circular. The way the end blocks and washers ride on the rail make it so that it need not be super-accurate in terms of its "circularity" but does have to be close enough to look right. Adjust and then glued it down with something like Goo, your favorite flexible adhesive or use spikes.  Completing the bridge for now are whatever cosmetic treatments you apply to the bridge. Mine are scrapbox specials, plastic girders over a wood substructure, but modeling to prototype will also work.  
|
|
|
Post by mlehman on May 25, 2015 8:10:56 GMT -8
It all looks really nice together, but... that pit looks like a band new concrete slab. Need some stains and drippings down in there my friend. Just a thought. :-)> True, all in good time. Adding weeds has to be done carefully to not hangup on things, etc, so I do this last. As you can see by the first pit, it'll get trashier looking. 
|
|
|
Post by mrsocal on May 25, 2015 9:35:03 GMT -8
Cool and you do very nice work too.
|
|
|
Post by mlehman on May 25, 2015 9:56:03 GMT -8
This pic shows several aspects of construction nicely at this stage. Note the two wires coming out of the upper surface, the leads from the phono plug.  If you look closely, you can see how I built up the bridge because I was running low on long girders. If one is working from a prototype, then you want to get as close a version as you can, but free-lancing simply calls for it to be believable. Given it'll be painted black and mostly hidden in the overhanging shadows from above, I wasn't too picky here. Obviously a lot more care and attention to specific details would yield impressive results. Finally, the thin bright sheet of basswood laid on top. It's part of my method to get close enough and then shim things. Some things really need to be done right, like getting the pit floor level. This allows things to stay level as you build you pit walls and for each side of the TT to be even. By the time I added in the cork roadbed coming in from the finger tracks, I ended up with the surface of the bridge about 1/32" below the top of the cork. This ain't perfect, but it's good. If you end up taller than the pit edge with the bridge, it's a real PITA to adjust that little bit. Now, I could've adjusted the jack the plug goes into, but that would've been difficult in this case because the limited depth available here made it more sensible to just leave things as they were. Otherwise, keep that as an adjustment in mind when getting the bridge and pit edge level all around with each other. Instead, just much easier to shim things here with the 1/32 basswood. It'll all be covered with decking later anyway. The wires are again threaded through this layer before gluing it down.
|
|
|
Post by bar on May 25, 2015 11:45:32 GMT -8
Nice change to see a cheap 'n' easy project here, from the usual engine and car threads. Thanks, Mike!
|
|
|
Post by brotherlove on May 25, 2015 11:57:11 GMT -8
I wish I needed a turntable on my layout so I could build one too. Great build! Malcolm
|
|
|
Post by bnsf971 on May 25, 2015 13:54:13 GMT -8
Terry, This is an eco-friendly, 100% zero emissions, and sustainable turntable. No blenders, etc, just your finger powers it. For the perpetually dissatisfied and grouchy among us, use of the middle finger is allowed (although only off-camera, please!). . I just thought I'd remind you about your covered turntable that sounded like a blender...
|
|
|
Post by mlehman on May 26, 2015 0:04:51 GMT -8
Thanks for the comments everyone.
bar, I like cheap and easy. I spend my money on Blackstone, track, and Tortoises. Going need to rebuild kit inventory one of these days. But I just like building stuff. I'll have to think of sequel.
Malcolm, Never know when you might need a TT, although modern RRing doesn't have many. I think you could build a 90 footer like this. Modules are another example, as these sorts of TTs are really popular with the modular crowd, as you can pop the bridge out for safekeeping and you're good to go, plus no complicated drives. Solid reliability.
|
|
|
Post by mlehman on May 26, 2015 0:10:24 GMT -8
Terry, This is an eco-friendly, 100% zero emissions, and sustainable turntable. No blenders, etc, just your finger powers it. For the perpetually dissatisfied and grouchy among us, use of the middle finger is allowed (although only off-camera, please!). . I just thought I'd remind you about your covered turntable that sounded like a blender... Ah, now I know what you were referring to.  Yeah, I'm kinda stuck with that one. It's too far away to reach in and you can't see to align the rails anyway, so no way to sub one of these silent drive models for its raucous behavior. The Geneva drive on the Atlas uis absolutely reliable and trustworthy. It's magic how they come back out of the snowshedI thought Atlas came out with a quieter drive, if so may try that. That's a limit with these TTs, as they need to be within easy reach and good sightlines to see the rails align. There's still a place for the Atlas here because of the special characteristics.
|
|
|
Post by bnsf971 on May 26, 2015 3:54:25 GMT -8
Mike, the new turntable drives use a belt, instead of gears. At least, that's what the picture on the box shows. I don't know how long a rubber belt would last, if access is a problem.
|
|
|
Post by dtinut on May 26, 2015 5:25:06 GMT -8
Mike,
Nice write-up on the TT. Looks good, and pretty simple. Thanks for taking the time to explain your work.
Brian
|
|
|
Post by mlehman on May 26, 2015 8:17:34 GMT -8
Mike, the new turntable drives use a belt, instead of gears. At least, that's what the picture on the box shows. I don't know how long a rubber belt would last, if access is a problem. Terry, Maintenance access is OK, it's just too much reachover for ops to deal with. Then there's the matter of the snowshed in the way...  A belt drive sounds like the cat's pajamas and would substantially cut noise. I wonder if it's compatible with the older Atlas TTs or if I'd need to buy another and convert it? That wouldn't be a problem, they're cheap enough, just not less than $20  Brian, Thanks, glad to add to our knowledge base here. Hoping to get to another update later today.
|
|
|
Post by bnsf971 on May 26, 2015 8:51:04 GMT -8
Mike, they looked like a direct screw-in swap. Two wires nd two machine screws, and you're in business. Just remember, all I did was look at the box and read the stuff printed on it.
|
|
|
Post by mlehman on May 26, 2015 10:33:17 GMT -8
Terry, Looks like a drop-in in the online instructions, too. I may have to try this when finances allow. The old one doesn't get used much, but it's loud enough that people fear using it. 
|
|
|
Post by mlehman on May 27, 2015 17:41:36 GMT -8
My computer ate the first attempt at an update this afternoon. Let's see how this goes.  This pic illustrates one of the more difficult features of building a turntable and as a means to check it for circularity. In other words, does the bridge line up to connect two tracks at BOTH ends even after turning the bridge 180 degrees? You generally want this to happen so when the bridge is lined for the lead track there is a safety overrun into the finger track opposite to the lead track. Beyond that issue, being able to do this indicates whether your bridge is accurate and square enough to use. If the bridge track isn't centered and straight along its length, now is the time to adjust. Although we already did most of the work building the bridge, keep in mind you need to leave an opportunity to check it for squareness, etc in order to correct them BEFORE you finalize the TT bridge. Once you can 180 the bridge consistently, then you're ready to do two more things. First, finish the bridge finalizing the revisions, if any. Second, use the verified bridge in order to check the TT end of each service track Here's my new TT bridge with the track and deck installed.  Since the deck hides the track underneath, you have to make a decision about how to handle that. Even if you handlay, getting it exactly centered when it's done is a pretty good trick. That why I prefer RTR track for this. On my first TT, I used a pair of M-E bridge track segments, leaving the tie ends exposed and soldered back to back. On the second, I covered it all, simply using a segment of plain ol' flex carefully centered and soldered to the power leads. Gets everything right and centered with a little care. At this point, you start checking all the other finger tracks and adjust height as needed. Either shim up a little or shave off to lower to match the bridge, which by this time should be running straight and true vs the ends of the rail varying up and down.
|
|
|
Post by mlehman on May 28, 2015 9:22:54 GMT -8
Since things were in pretty good shape during the construction phase, I actually skipped undercutting and shimming until right at the end. Most tracks lined up well enough. Here's what I did to bring things to final level. The first pic shows how I undercut the track into the enginehouse to level it. It was just a little high. In this case, the first tie rested on the pit wall. I tend to let things fall where they may with that, but you may find it advantageous to have all or none sitting like this, as you can see in these three pics. I simply shaved underneath with a knife blade until things were level. Don't forgether the nee to be level side to side, as well as end to end.  Then I stained the pit wall where I trimmed, so that gouging disappeared. On the other two track ends here I used styrene shims to bring them up a little. Easier to see unpainted, I';; deal with that later.  And the other side and its leveling. 
|
|